Contents
Serialization System / Aggregation System (For Track & Trace)
What is Track & Trace?
Track & Trace is a term used in logistics activity. Tracking is to identify current situation (location, status, etc) of the object in a supply chain. Tracing is to identify situation of the object at a certain time in the past by going back the way it went through. In recent years, pharmaceutical industry is accelerating the discussion how to lockout counterfeit drugs, and Track & Trace has drawn attention as one of effective countermeasures.
「Serialization」 is an essential part of Track & Trace
Serialization is one of integral elements which realize Track & Trace. It means to assign a unique serial number to each item individually. A representative example is tracking number shown on a slip of courier service. Every parcel is assigned with a unique number so that we can identify and locate (=track) the specific parcel.
「Aggregation」 is a concept developed from serialization
Aggregation means to “link” serial numbers assigned to smaller packages (=children) to a serial number assigned to a larger package (=parent) which contains the children.
For example with PTP sheet of tablets,
Unique serial numbers are issued and labelled individually on “cartons”, each of which contains 10 x PTP sheet of tablet. Next, 5 x cartons are bundled into a larger package called “case”, and a new serial number is issued and labelled on the case. The serial number of the case (parent) and serial numbers of the 5 cartons inside (children) are linked together, and that linked data is recorded and saved. By repeating this process to the final package for shipping, complete relationship between parent and children will be saved in a database, which enables you to immediately locate a specific package by searching for the serial number in the database.
Track & Trace in the world
A WHO report of November 2017 tells that one medicinal product out of ten on a market in low-mid income countries are counterfeit drug or genuine drug but not meeting quality requirement. In recent years, on the initiative of developed countries, serialization and registration to national database has become mandatory worldwide. Some countries have fully implemented the system by legislation, and the others are busy in preparation before their law shortly takes effect. Japan, being thought to be a nation with “zero counterfeit drug in the market” for a long time, was shocked by the incident in 2017 that a pharmacy unknowingly sold to patient a counterfeit drug for hepatitis C treatment, which was the first case that fake drug was discovered in a formal drug supply chain.
Being sparked by this incident, Japan has started to actively discuss possible countermeasures against fake drugs even with an eye to implementation of Track & Trace system in future.
Advantages for drug manufacturers
How does Track & Trace system work in the pioneering countries? In a drug manufacturing process, individual package is labelled with a unique identification code (Note 1) and those codes are registered in a database which is run by nation. After shipment, those codes are read by code readers at various points of supply chain and referenced to the code data already registered in the database. By this, counterfeit drug is immediately detected and retrieved because no matching code is found in the database. Once Track & Trace system is thoroughly implemented nationwide, all electrical data of specific product, including which route it went through on the supply chain and even which patient finally consumed it, can be tracked and traced.
(Note 1:Unique identification code normally contains such data as product name, lot/batch number, expiry date and serial numbers. However, what data is to be labeled on what package level of what type of drug differs from country to country.)
Any advantage for pharmaceutical manufacturer?
Anti-counterfeiting
- Unique identification code is read at many points in the supply chain and referenced with the code registered in the database. If the code does not match or is duplicated, the product is immediately judged as a fake product.
- In case of theft, precise identification of stolen drugs will eliminate risk of resale or counterfeiting.
- Labelling a unique code on package itself has an effect to discourage counterfeiting.
- Eliminates the risk of sales loss of genuine product, loss of trusted brand image, tremendous recall activity, etc.
Improved productivity
- Higher recall efficiency in case of defects (Quick identification of location and status of recalled products, and quick information sharing)
- Every event of a specific product can be traceable in case of defect
- Eliminates mix-ups in shipping → Streamlined distribution
- Comprehensive management and analysis of data from production to distribution → Improvement in production/distribution plans
Serialization System (HIES-5000SZ)
This system controls GS1 codes and human readable texts for pharmaceutical packages, communicates print data and inspection data with connected printers and inspection machines, and records and retains the printing and inspection results.
This system is co-developed by Kanadevia Corp. (former Hitachi Zosen Corp.) and ease LIMITED.
Advantages
- Made in Japan (Easy operation with Japanese language. Responsive after-sales service)
- NO annual license fee (Less running cost)
- Provides a full set of validation documents from System Assessment to IQ/OQ
- Complies with current Track and Trace regulation of target country. Swift response to regulation updates.
- Installable for both new and existing lines
- Versatile for future addition of new products and target countries
- Future expansion into Aggregation System HIES-7000AG
- Consolidated management of production log data etc. by connecting with PLC and various systems.
- Communication with TraceLink Life Sciences Cloud® services
Please call or email our experienced engineers for an optimized design proposal including complete packaging line.
Installation Example
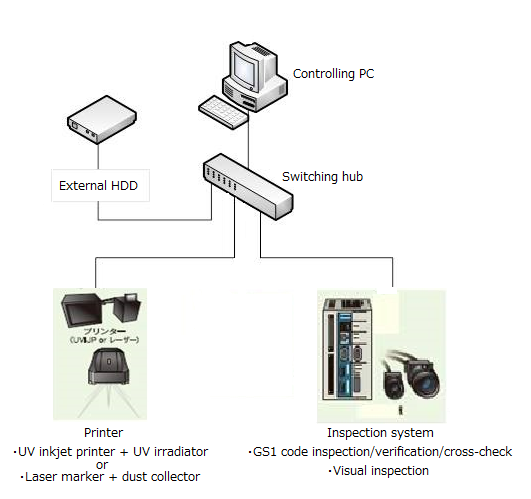
Functions
- Serial number data management
Generates and controls unique serial numbers to be assigned to each package - Print and inspection
Sends print data to the connected printer → Prints → Sends inspection command to the inspection machine (inspection/verification/cross-check) → Receives inspection result - Log data management
Outputs print data in CSV (readable in Excel) and PDF format - Master data management
Retains master data of product type, print format or text for each drug product, etc - ER/ES
Complies with 3-hierarchized ID/Password and audit trail
Maximum effect by minimum effort
Do not worry if you are concerned about modification of existing line in order to accommodate Serialization System. Our system is highly extensible and easily incorporated into existing production lines. Serialization system has a number of comprehensive advantages. High consistency in the drug supply chain not only enhances compliance, reverse logistics control and recall efficiency, but also leads to more accuracy of forecast and even to establishment of customer-specific marketing program. Keep your attention to such various advantages. Serialization System has immense potential.
References
Pharmaceutical manufacturer “S”
Pharmaceutical manufacturer “Y”
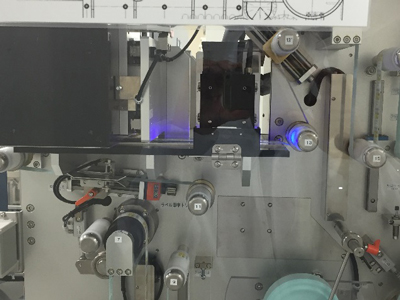
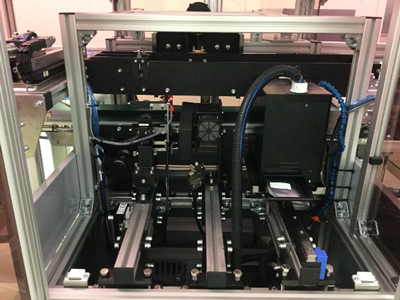
Aggregation System (HIES-7000AG)
In addition to the functions of Serialization System HIES-5000SZ, this system aggregates pharmaceutical packages – between the smallest packaging unit “carton” (primary code), case (secondary code) and shipping case (tertiary code). Aggregated data is recorded and output to arbitrary folder in PDF, XML or CSV format.
This system is co-developed by Kanadevia Corp. (former Hitachi Zosen Corp.) and ease LIMITED.
Advantages
- Made in Japan (Easy operation with Japanese language. Responsive after-sales service)
- NO annual license fee (Less running cost)
- Provides a full set of validation documents from System Assessment to IQ/OQ
- Complies with current Track and Trace regulation of target country. Swift response to regulation updates.
- Installable for both new and existing lines
- Versatile for future addition of new products and target countries
- Future integration to Serialization System HIES-5000SZ
- Consolidated management of production log data etc. by connecting with PLC and various systems.
- Communication with TraceLink Life Sciences Cloud® services
Please call or email our experienced engineers for an optimized design proposal including complete packaging line.
Installation Example
System flow overview
Serial numbers which are labelled on each carton (primary code) are read one by one or simultaneously until the reading reaches a pre-set quantity.
When reading of the primary codes is done, a secondary code (new serial number) is generated and issued on a label.
Sticker the label on the case (secondary package)
The secondary code on the case is read and linked to the primary codes of the contained cartons.
Repeat above procedures and put those cases into a shipping case (tertiary package)
Serial numbers labelled on each case (secondary code) inside the shipping case are read one by one or simultaneously until the reading reaches a pre-set quantity.
When reading of the secondary codes is done, a tertiary code (new serial number) is generated and issued on a label.
Sticker the label on the shipping case (tertiary package)
The tertiary code on the shipping case is read and linked to the secondary codes on the contained cases.
Functions
- Data management
Database manages all data which is handled inside this system. - Import of codes
Codes for carton, case and shipping case are taken into the system and registered.
Compliant to various GS1 codes for pharmaceutical labelling. Automatic generation of codes is also possible. - Creates a packaging plan
Creation of packaging plans is possible. - Perform a packaging plan
①Reads primary codes on cartons (one by one or simultaneously) for the pre-set quantity, and issues a secondary code label and stickers it on a case (secondary package).
②Reads the stickered secondary code, and aggregate it to the already read primary codes only if both codes are confirmed valid.
③Reads the secondary codes on cases (one by one or simultaneously) for the pre-set quantity, and issues a tertiary code label and stickers it on a shipping case (tertiary package).
④Reads the stickered tertiary code, and aggregate it to the already read secondary codes only if both codes are confirmed valid. - Master data management
Retains master data of product type, print format or text for each drug product, etc. - Output of aggregated data
Result of aggregation between cartons (primary code), cases (secondary code) and shipping cases (tertiary code) can be output as a file in PDF, XML or CSV format. - Coordination with Serialization System
Product master data, user master data can be shared by communication with Module Controller PC.
References
Pharmaceutical manufacturer “S”
Primary codes (on carton) are read, and secondary code labels (for case) are issued and stickered in this area. In this case, 10 x cartons are simply bundled (without a case). All 10 codes are read simultaneously at once, and the label of secondary code is stickered on a surface of the bundle.
Ease Limited provides highly customized Serialization/Aggregation Systems according to various country-specific regulations. Feel free to contact us.